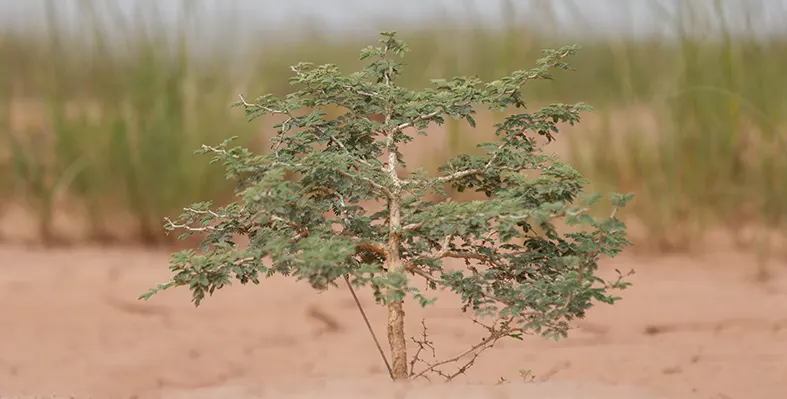
Horizontal nozzle-pressurised spinning could be a huge boost to the global dairy farming industry. (Image source: UCL)
Researchers have developed a new technique to extract tiny cellulose strands from cow dung and turn them into manufacturing-grade cellulose
A study published in The Journal of Cleaner Production, describes the potential of a new ‘pressurised spinning’ innovation that uses cow dung as a raw material to create cellulose materials more cheaply and cleanly than some current manufacturing methods. Cellulose is one of the world’s most commonly used manufacturing materials, and can be found in everything from cling film to surgical masks, paper products, textiles, foods and pharmaceuticals.
Professor Edirisinghe, the senior author of the study, considered the possibility of extracting tiny fragments of cellulose present in cow manure and turning it into manufacturing-grade cellulose materials. He first used mild chemical reactions and homogenisation, which was successful in fragment extraction. However, the use of pressurised spinning technology to turn these fragments into fibres failed.
However, upon trial and error, a new technique called horizontal nozzle-pressurised spinning, proved successful. This is an energy efficient process that doesn’t require the high voltages of other fibre production techniques such as electrospinning. This advancement is a prime example of circular economy and is the first time that manufacturing-grade cellulose has been derived from animal waste.
Horizontal nozzle-pressurised spinning could be a huge boost to the global dairy farming industry, given the fact that animal waste management continues to be a growing problem globally. The research team is currently seeking opportunities to work with dairy farmers to take advantage of the technology and scale it up.