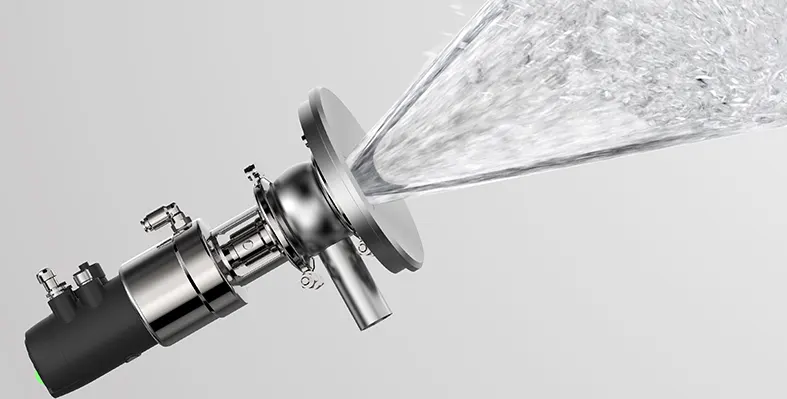
GEA Direct Sprayer DS 25 delivering powerful cleaning performance with five kilograms of spray force and a full-cone jet reaching up to five metres. (Image source: GEA)
GEA has introduced its new patented technology – the GEA Direct Sprayer DS 25 – for industrial tank cleaning in the food and beverage industry
The patented spray technology effectively removes residues from the undersides of agitators, pipes, and flow breakers. It has been developed for use in the beverage, food, dairy, pharmaceutical, and home and personal care industries, and is particularly advantageous in production environments with frequent recipe changes, strict hygiene standards, and demanding cleaning requirements.
In the food and beverage industry, cleaning tanks with internal installations often go through a major challenge. The undersides of agitator blades being in the spray shadow, prevents them from being adequately cleaned by conventional methods. This is where the Direct Sprayer DS 25 comes into picture. This technology sprays directly onto the undersides of the agitator blades while ensuring that the agitator mechanics remain unaffected. The cleaner is flush-mounted into the tank wall and can be positioned flexibly, ensuring full coverage inside the tank. The patented valve disc only opens when activated, ensuring an even distribution of the cleaning fluid. Since the valve plate opens inward, it does not interfere with the agitator.
The mechanically powerful full-cone spray targets the undersides of the agitators and efficiently removes residues. While conventional cleaning systems operate at lower forces, the GEA Direct Sprayer DS 25 operates with a spray force of up to 5 kg, allowing it to remove even tough residues. A case study from yogurt production has revealed the ability of the GEA Direct Sprayer DS 25 technology to reduce water usage by 84.5% and cleaning time by 87.5%, making it one of the most efficient cleaning methods for tanks with agitators.
“This time saving can be directly used for additional production capacity,” explained product sales manager for Cleaning Technology at GEA, Jana Zimpel. “In yogurt production, for example, this means more batches per day or faster recipe changes without compromising efficiency.”