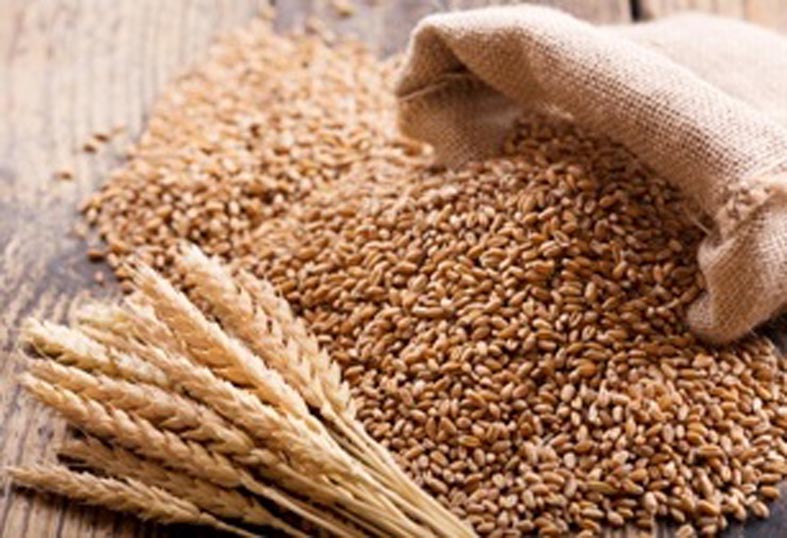
The project is designed to validate wheat germ cell-free protein synthesis as a rapid and affordable approach to drug development. (Image source: Adobe Stock)
Wamego-based company, Tritica Biosciences, along with three other partners have joined hands to work under Boston-based Ginkgo Bioworks, on a million-dollar project aimed at exploring the potential of the wheat crop in transforming drug development
The project is designed to validate wheat germ cell-free protein synthesis as a rapid and affordable approach to drug development. This powerful innovation introduces a new method of biomanufacturing that has broad applications across various sectors ranging from food to pharmaceuticals.
The ARPA-H project, known as Wheat-based High efficiency Enzyme and API Technology (WHEAT) is one of the first initiatives within ARPA-H’s Scalable Solutions Office, which aims to transform the health by improving the speed, scale and access to medical treatments.
The project aims to boost domestic manufacturing of critical medicines by producing them when and where they are needed. Many active pharmaceutical ingredients (APIs) are currently affected by fragile global supply chains, and reshoring biomanufacturing will help stabilise the supply of critical, life-saving drugs.
According to a news release from Ginkgo Bioworks, WHEAT’s innovations will include post-translational modifications to establish a foundation suitable for producing biologics.
“By harnessing the power of wheat based cell-free systems, we’re planting the future of medicine, helping to make production more efficient, flexible and localised,” said Dr Chris Miller, founder and CSO, Tritica Biosciences.