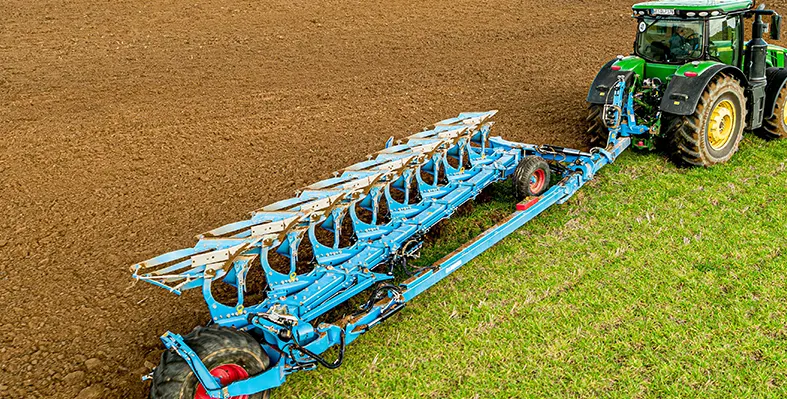
One of the main advantages of the new wheel positioning is the lower centre of gravity which allows the plough to be subjected to lower rotational forces, in turn resulting in less strain on the rear lift. (Image source: LEMKEN)
Following the launch of the LEMKEN Diament 16 that was launched six years ago, the new Diament 18 model was presented at EIMA 2024 that took place from 6-10 November in Bologna, Italy
Being a key tool for large agricultural businesses, semi-mounted reversible ploughs, are increasingly used for both traditional in-furrow and on-land ploughing. Often used either as a stand-alone machine or in combination with a furrow press, the Diament series has always offered a wide range of applications to meet individual farm requirements for shallow or deep tillage.
To demonstrate that the Diamant plough series continues to stand for power and reliability, LEMKEN presented a new model at EIMA in Bologna: Diament 18 which enables the plough specialist to address an additional target group.
With its 5 to 8 furrows and a solid 180 x 180 x 12.5 mm box section frame, the robust Diamant 18 is specially designed for large tractors up to 650 hp and extreme operating conditions. Thanks to its optimum soil penetration and stable design, the new LEMKEN plough exhibits exceptional performance particularly on dry soils. The position of the support wheel has been conveniently updated in order to ensure ideal usage of the extra frame weight, thereby allowing reliable soil penetration and maintaining desirable and consistent working depth.
One of the main advantages of the new wheel positioning is the lower centre of gravity which allows the plough to be subjected to lower rotational forces, in turn resulting in less strain on the rear lift. The protects the plough components, while also ensuring high tipping stability of the tractor/plough combination and a smooth ride. In comparison to the Diament 16, the new model also offers agility and comfortable handling, owing to the innovative steering system for the transport wheel.
The transport wheel also has a hydraulic steering which automatically adapts the steering angle to the turning manoeuvre. In combination with the 90 degree steering angle on the plough headstock, this feature enables the smallest possible turning radii at the headland. Moreover, the transport wheel can be actively controlled and manually steered for manoeuvring work.
The Diament 18 will initailly be available in small quantities from next year and will begin full series production in 2026.